Влияние центробежно-ударного способа рудоподготовки на процесс обогащения полезных ископаемых
Одной из главных проблем, стоящих сегодня перед горно-добывающей промышленностью, является снижение издержек на подготовку руды перед обогащением. При этом особое внимание уделяется качеству получаемых продуктов. Это заставляет искать новые способы разрушения горных пород, к которым можно отнести центробежно-ударный. Л.Ф. Биленко, А.В. Лисица, В.И. Лисица Одной из главных
проблем, стоящих сегодня перед горно-добывающей промышленностью,
является снижение издержек на подготовку руды перед обогащением. При
этом особое внимание уделяется качеству получаемых продуктов. Это
заставляет искать новые способы разрушения горных пород, к которым
можно отнести центробежно-ударный. Дробление и измельчение
рудных минералов традиционными способами (конусные дробилки, щековые
дробилки, шаровые мельницы) обладает по сравнению с ударным разрушением
значительно более низкой селективностью и более высокой степенью
шламообразования, что ведет к ухудшению параметров дальнейшего
обогащения. Дробление материалов в дробилках ударного действия
производится за счет высокой центробежной силы, которая перемещает
загружаемый материал и направляет его на отражательную плиту или пласт
из измельченной породы в камере дробления. Происходит разрушение в
основном вдоль линий естественного разлома или по плоскостям срастания
минералов. Продукты измельчения имеют кубовидную форму, что облегчает в
частности дальнейшую его классификацию. Размер готового продукта может
регулироваться изменением частоты вращения ускорителя и конструкцией
встроенных в центробежную мельницу воздушных классификаторов.
Недоизмельченный продукт возвращается обратно в мельницу для
дальнейшего измельчения. Хотя разрушение свободным ударом начали
применять на практике достаточно давно (более 20 лет назад),
центробежные дробилки нашли широкое применение преимущественно в
процессах производства щебня. Это может быть объяснено ненадежностью
первых образцов центробежных дробилок. В первую очередь это относится к
опорным узлам роторных систем, что влечет за собой чувствительность к
дисбалансам, основанным на подшипниках. Как следствие, такие системы не
могут вращать большие массы с высокими скоростями. Долгое время
нерешенным был вопрос с износом рабочих органов дробилки. В
результате, выпускаемые в настоящее время дробилки имеют ряд
ограничений, таких как крупность исходного питания до 50 – 60 мм,
диаметр ротора не более 1 м и соответственно скорость вращения до 60 –
70 м/с для больших типоразмеров. Данные ограничения не позволяют
эффективно заменить конусные дробилки мелкого дробления в существующих
схемах. Одна из ведущих российских фирм по добыче благородных
металлов - ОАО Полиметалл - стала инициатором создания компании ЗАО
Новые технологии, научно-технические и машиностроительные разработки
которой являются продолжением исследований, начатых в 1980-90 г.г. в
рамках программ Минсредмаша. Исследования, выполненные силами этих
специалистов, позволили решить проблемы, о которых говорилось выше. Для
этого в конструкции центробежных машин была применена так называемая
воздушная опора вращающегося ротора, использование которой позволило
увеличить допустимый дисбаланс в 10 раз по сравнению с системами,
основанными на подшипниках. Это, в свою очередь, дало возможность
разработать уникальные в своем роде центробежно-ударные мельницы,
которые делают возможным измельчение до 40 – 50 мкм. При этом за счет
отсутствия передачи вибраций на корпус оборудование не требует
массивных оснований, может быть смонтировано на любой отметке
производственного здания и отличается самой низкой материалоемкостью в
своем классе (рис.1.).
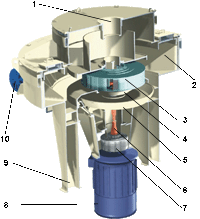 | 1. Загрузочная воронка
2. Камера измельчения с самофутеровкой
3. Ускоритель
4. Демпферный узел
5. Воздушная опора
6. Карданный вал
7. Центробежная муфта
8. Электродвигатель
9. Выгрузка дробленого материала
10.Вентилятор наддува |
Рис.1. Схематичная модель центробежной дробилки Титан Д
Последние достижения науки в области износостойких футеровок, а также в
создании узлов, позволяющих работать на больших скоростях, привели к
все большему применению центробежных дробилок и мельниц в
подготовительных процессах обогатительных фабрик. Так, на
золотодобывающих установках МНПО "Полиметалл" в основном используется
обогащение методом кучного выщелачивания, что требует применять сухие
способы рудоподготовки. Центробежно-ударное измельчение всухую в данном
случае становится практически безальтернативным. Сегодня дробилки и
мельницы ЗАО Новые технологии находят применение в подготовительных
процессах на месторождениях Барун-Холба, Воронцовское, Дукат и ряде
других. С помощью них можно существенно снизить крупность питания,
поступающего на измельчение, а в отдельных случаях, при сопоставимых
энергозатратах, даже полностью заменить шаровые мельницы на
центробежные (рис.2.). 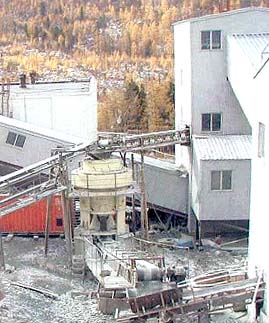 Рис.2.
Дробилка Титан Д-160 в схеме измельчения золотодобывающего предприятия
«Зун-Хада» для снижения крупности питания до 5 мм перед шаровой
мельницей (Полиметалл) ЗАО Новые технологии производит дробилки и
мельницы с роторами от 0,36 до 2,5 м, с возможностью варьирования
скоростей от 40 до 100 м/с на всех типоразмерах, с производительностью
в открытом цикле от 1 до 650 т/ч. Установка дробилки в замкнутый цикл с
воздушными классификаторои, также выпускаемыми фирмой, дает возможность
получать материал флотационной крупности. За счет исключительной
легкости замены быстроизнашиваемых элементов (время замены ускорителя
не превышает 1 ч двумя рабочими) КИО оборудования составляет не менее
0,85. При этом удельные затраты на сами быстроизнашиваемые элементы
(ускоритель) составляют около 0,017-0,03 долл. США на тонну
перерабатываемого материала. Повышение скоростей дробления до 80 – 100
м/с позволило выйти на качественно новый уровень. Проведенные
промышленные испытания установили, что при дроблении руд крепостью до
20 по Протодьяконову и крупностью до 100 мм степень сокращения
достигает 15-20 при расходе электроэнергии до 3,0 кВт/ч на тонну. При
этом, несмотря на повышенный расход электроэнергии, повышается на
20-30% производительность дальнейшего измельчения за счет более низкой
крупности исходных продуктов дробления и, как следствие, значительно
снижаются общие энергозатраты на рудоподготовку (рис.3). 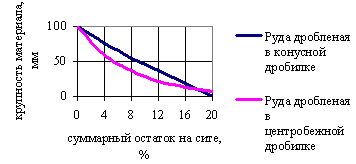 Рис.3. Характеристика крупности пробы дроблённой железной руды
Однако основные преимущества центробежно-ударного измельчения
заключаются в том, что разрушение минералов происходит по местам
срастания минералов, то есть этот метод разрушения обладает высокой
селективностью раскрытия при более грубом помоле, что имеет решающее
значение при дальнейшем обогащении и позволяет начинать его на более
ранних стадиях измельчения (при большей крупности). При этом, дробление
и измельчение ведется всухую, что значительно снижает затраты на
рудоподготовку, а в ряде случаев позволяет и обогащение вести сухим
способом. Так, например, сухое обогащение карбонатных марганцевых руд
Полуночного месторождения (Северный Урал) позволило получить концентрат
с содержанием марганца не менее 30% при 19% содержании в исходной руде
[1]. При этом извлечение марганца в концентрат составило 79% и 8%
содержание в хвостах обогащения. Опробование этой технологии на
окисленных марганцевых рудах Северо-Казахстанского региона показало
возможность получения концентрата с содержанием марганца более 40% (в
исходной руде до 14%), при его извлечении в концентрат не ниже 70% и
содержании марганца в хвостах около 6%. Исследования, проведенные на
железистых кварцитах Михайловского ГОКа, показали, что при центробежном
измельчении до 80% класса –0,074 мм существенно вырастают показатели
обогащения. Это достигалось не только за счет увеличения селективности
раскрытия, но и за счет уменьшения шламообразования. Испытания
Титаномагнетитовых руд дробленных на центробежно-ударной дробилке на
обогатимость показали возможность сброса в хвосты на стадии сухой
магнитной сепарации в отдельных опытах до 40% руды против 15% по
существующей технологии (дробление в конусных дробилках). Это позволит
значительно снизить затраты на дальнейшее измельчение. В настоящее
время на Качканарском ГОКе установлена центробежно-ударная дробилка
Титан Д-250 вместо стержневой мельницы. Первые испытания показали
высокую степень дробления руды (до 76% класса –1,6 мм) (рис.4.). 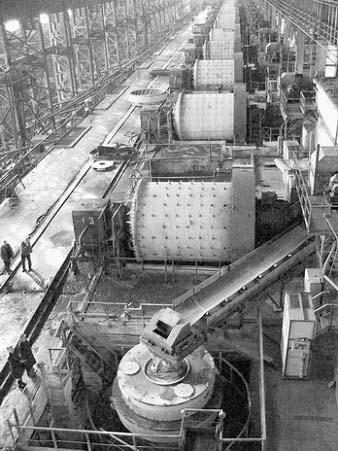 Рис.4. Дробилка Титан Д установлена в схеме Качканарского ГОКа Вышеприведенные данные подтверждаются также исследованиями, проведенными институтом Механобр (г. Санкт-Петербург) на медно-сульфидных и вольфрамомолибденовых рудах [2]. Руды готовились к обогащению тремя способами: 1.
исходная руда 30-0 мм дробилась в центробежно-ударной дробилке и
измельчалась в центробежной мельнице до крупности 70% класса –0,074 мм; 2.
исходная руда 30-0 мм дробилась в центробежно-ударной дробилке и
измельчалась в шаровой мельнице до крупности 70% класса –0,074 мм; 3. исходная руда 30-0 мм дробилась в валковой дробилке и измельчалась в шаровой мельнице до крупности 70% класса –0,074 мм. Минералогический
анализ медной руды, измельченной до одинаковой крупности, показал, что
раскрытие минеральных сростков значительно лучше происходит при
разрушении свободным ударом. Содержание раскрытых сростков халькопирита
в классе более 0,16 мм при центробежно-ударном разрушении составляло от
80 до 95%, в то время как при стандартном способе измельчения оно
снижалось до 55-60%. Содержание свободных зерен пирита в классе
крупности более 0,16 мм при ударной дезинтеграции составляло 85% против
75% при стандартном разрушении. Подобная тенденция наблюдается и для
других классов крупности минералов. При комбинированном способе
измельчения (ударное дробление, шаровое измельчение) степень раскрытия
сростков была ниже, чем при центробежно-ударном способе измельчения, но
выше, чем при традиционном способе дезинтеграции. Проведенные
исследования показали, что наиболее высокие результаты получены при
флотации руды, подготовленной к обогащению ударным способом. Концентрат
содержал 16,5% меди при извлечении 78,9%, хвосты содержали 0,09% меди.
При обогащении руды, подготовленной к флотации стандартным способом,
содержание меди в концентрате составляло всего лишь 10,6% при
извлечении 69,9%. Комбинированный способ измельчения также обеспечивал
хорошие результаты при флотации. Содержание меди в концентрате
составило 17,0%. Это можно объяснить тем, что в процессе
центробежно-ударного измельчения образуются макро- и микротрещины по
линиям срастания минералов, по которым происходит разрушение при
измельчении в шаровой мельнице [2]. При флотационном обогащении
вольфрамомолибденовой руды, подготовленной традиционным способом,
получен концентрат с содержанием молибдена 1,1% при извлечении 84,8%.
При центробежно-ударной дезинтеграции за счет повышения селективности
раскрытия получается более качественный концентрат (содержание
молибдена 1,3%) при лучшем извлечении – 89,3%. Комбинированная
схема рудоподготовки вольфрамомолибденовой руды, так же как и в случае
с медной рудой, улучшает результаты обогащения по сравнению с
традиционными способами [2]. Таким образом, наряду с
центробежно-ударным способом измельчения перспективным также является
комбинированный способ подготовки руд (центробежно-ударное дробление и
шаровое измельчение), который обеспечивает как повышение
производительности измельчительного передела, так и повышение
селективности раскрытия минералов и как следствие улучшение показателей
обогащения. Литература 1. Патент №3245, «Способ обогащения марганцевой руды», Лисица А.В. и др., 23.10.99 г. 2. О предварительном разупрочнении руд и принципах селективного раскрытия минералов, - Л.Ф. Биленко; Обогащение руд, 1997, №5
Перепечатка данного материала приветствуется при следующих условиях: на сайт www.acma.ru будет поставлена
прямая, активная, нескриптовая, незакрытая от индексирования, не
запрещенная для роботов ссылка.
ссылка на данную статью-
Влияние центробежно-ударного способа рудоподготовки на процесс обогащения полезных ископаемых</a>
|
Коментарии к этой статье(2)